|
Prosthetic Hand Fabrication |
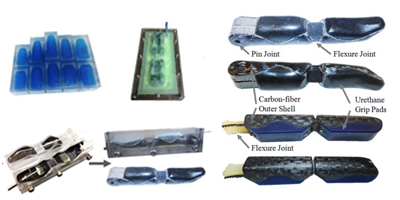
|
|
Additive manufacturing, or 3D printing, has become a widely accessible and cost-effective method of prototyping due to its ability to quickly create custom modeled parts out of inexpensive thermoplastics and resins. A common method of additive manufacturing, fused deposition modeling (FDM), uses an extruder head that lays down a filament in discretized layers to create a final part. The thermoplastic filament, acrylonitrile butadiene styrene (ABS), is commonly used in this process due to its high impact resistance, toughness, and light weight. This has made 3D printed ABS a prevalent choice for open-source prosthesis hands with products like the Cyborg-Beast or the Raptor Hand, which are intended to allow for a low-cost prosthesis that is also customizable. Although 3D printing has made custom prosthetic designs accessible to the public, it lacks the durability and strength to make these devices practical, which then have many shortcomings compared to commercially manufactured terminal devices. In our work, we investigate fabrication methods utilizing inexpensive 3D printing techniques to produce molds that are then used in multi-material molding processes to make stronger, lighter prosthetic hands.
Sample Publication:
Michael T. Leddy, Joseph T. Belter, Kevin D. Gemmell, and Aaron M. Dollar
Lightweight Custom Composite Prosthetic Components Using an Additive Manufacturing-based Molding Technique, proceedings of the 2015 International Conference of the IEEE Engineering in Medicine and Biology Society (EMBC 2015), Milan, Italy, 2015.
Prosthetics
FabricationTechniques
2015
All Fabrication Techniques Publications >>
|